Turbocharging Laboratory
Head of Laboratory: | Takács Richárd |
Phone: | +36-96-613-574 |
Mobile: | +36-20-353-7629 |
E-mail: | takacs.richard##kukac##sze.hu |
Website: | https://bmt.sze.hu |
Address: | 9026 Győr, Egyetem tér 1., JL/0.13. |
INTRODUCTION OF THE LABORATORY
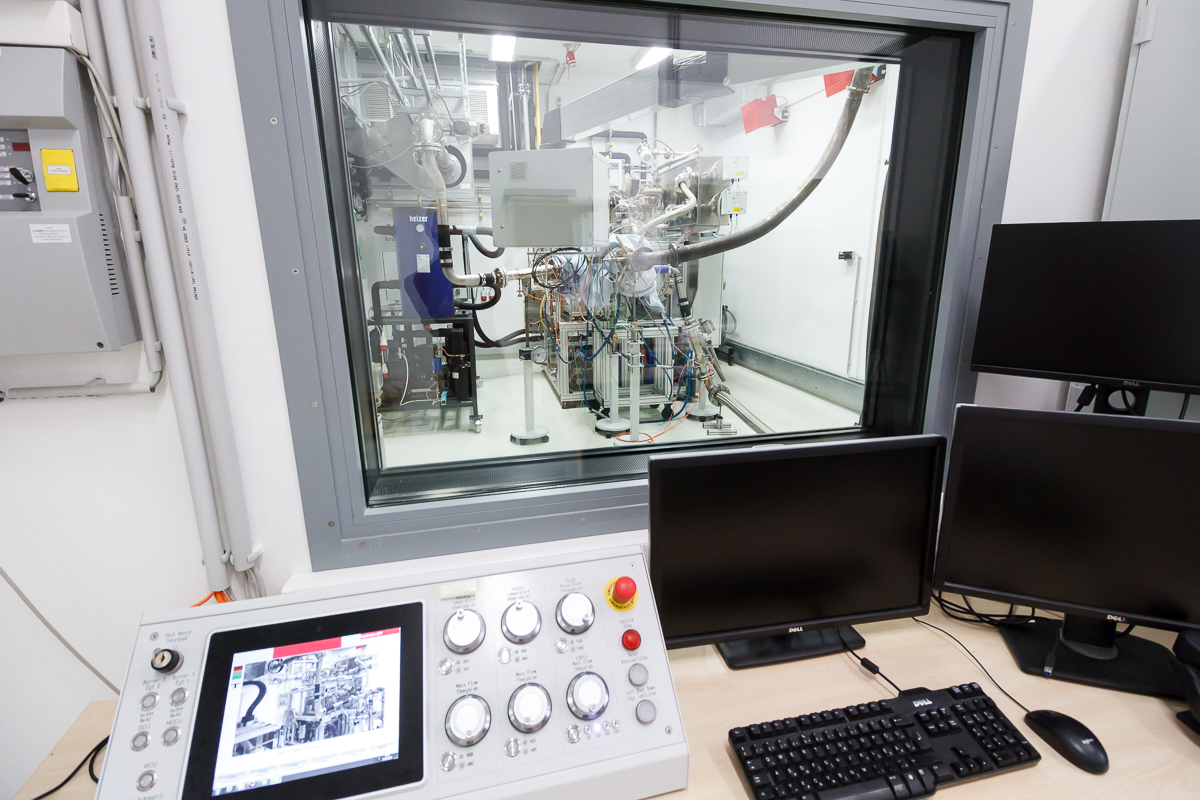
The Turbocharging Laboratory makes it possible to map the real conditions and loads of turbochargers of different sizes and types. Its main aim is to offer - specifically turbocharger-optimized measurements
and tests in a time- and cost-effective way. Using extremely precise control technology, the test bench provides the ability to create compressor / turbine maps as well as a wide range of temperature, pressure and other parameter settings. An outstanding potential is the
feasibility of dynamic, long-lasting heat loading processes, in which the maximum temperature value can reach 1200° C. All this can be done by installing two turbochargers of the same type at the same time. During this type of test, the material ageing process of turbine housing due to thermal fatigue can be observed. In order to examine the conditions and different loads of the multistage charging, the test bench has a specially developed unit with which a pressure and temperature control can be established in a wide range of volume flows. The test bench also allows controlling the lubrication and cooling system of the turbocharger. The backpressure of the exhaust systems of internal combustion engines can be simulated by integrating them directly into the so-called "backpressure unit" system after the turbine.
INTRODUCTION OF TESTS
Name of the test | The standard on which the test is based | Accredited test Y/N | Short description |
---|---|---|---|
Termo-sock | Not relevant | N | Investigation of structural changes in turbine blades under dynamic thermal loading. |
Oil consumption | Not relevant | N | Examination of emission standards and the provision of the necessary lubrication system. |
Map check | Not relevant | N | Recording and checking compressor and turbine characteristics. |
Saturation test | Not relevant | N | Sealing test of the entire turbocharger structure at different working points. |
Acoustic test | Not relevant | N | Research into noise emissions measured at different working points. |
Thermodynamic test | Not relevant | N | Investigation of high/dynamic thermal load of different types of turbochargers. |
Insufficient lubrication test | Not relevant | N | Research on simulating insufficient lubrication conditions. |
Life cycle test | Not relevant | N | Dynamic or constant duty point long duration test processes (hundreds of hours of continuous operation). |
Rotordynamic and bearing damage tests | Not relevant | N | Generation of critical rotordynamic states, life tests on these working points. |
Investigating the effects of particle abrasion on both compressor and turbine sides | Not relevant | N | Effect of the presence of injected abrasive particles on the turbine and compressor side. |
Blow-by analysis | Not relevant | N | Quantitative and qualitative characterisation of blow-by gases. |
Radio Nuclid Technology (RNT) measurements | Not relevant | N | Online wear measurement using an activated tool. |
Simulating multi-stage filling | Not relevant | N | Load and bearing testing of positive displacement compressors. |
If you have not found the right test or you would like to request a customised test, please contact us!
Takács Richárd
E-mail: takacs.richard@sze.hu
Phone:+36-96-631-574
Mobile:+36-20-353-7629
INTRODUCTION OF THE EQUIPMENTS
Name of the equipment | Parameters, test range | Inquiries/tests |
---|---|---|
Thermoshock unit (TSU) | - temperature: 20-1200°C - temperature gradient: >100°C/s - mass flow: 0,005-0,5kg/s |
Fatigue tests. |
Temosock Switching Unit (TSSU) | - temperature: 20-1050°C - temperature gradient: >150°C/s - mass flow: 0,005-0,5kg/s |
Simultaneous material fatigue tests on two turbochargers. |
Lubricating oil conditioning unit (OCUd) | - temperature: 20-150°C - flow rate: 0,2-5l/min |
Testing lubrication conditions and properties. |
Cooling water conditioning unit (WCU) | - temperature: 20-150°C - flow rate: 0,6-15l/min |
Turbocharger cooling system test. |
Compressor closed loop unit (CCLU) | - pressure: 1-6bar (compressor input) | Investigating the demands of multi-stage filling. |
Turbine back pressure unit (TBPU) | - pressure: 1-4bar | Impact assessment of exhaust system backpressure rating. |
Compressor back pressure unit (CBPU) | - pressure: 1-6bar | Compressor outlet side back pressure test. |
Compressor upstream pressure regulator unit (CUPU) | - pressure: 0,5-1bar | Making a compressor map. |
Suction air conditioning unit (SACU) | - temperature: 20-25°C | Temperature tests on the compressor inlet side. |
OTHER PROFESSIONAL COMPETENCIES/DEVELOPMENTS
COLLEAGUES
Name | Position | Scope of duties, main activities |
---|---|---|
Takács Richárd | Head of laboratory | Management of the laboratory. Test bench management, project support. |
Burkali Dávid | laboratory assistant | Test bench system support. |
REFERENCES
Audi Hungaria Zrt.